
Construction Applications
SIX STOREY APARTMENT BUILDINGS | LARGE MULTI-LEVEL RESIDENTIAL HOUSES
20 METRE SPAN WAREHOUSES | STORAGE FACILITIES | OFFICE BUILDINGS | WAREHOUSE EXTERNAL WALL IN-FILL FRAMING | HIGH RISE OFFICE BUILDING RAIN SCREEN SYSTEM SUPPORT WALLS | MODULAR BUILD | BATHROOM PODS | FLOOR JOISTS | BEAMS | ROOF TRUSSES
SFS MP200 Framer Standard Profiles (3) |
---|
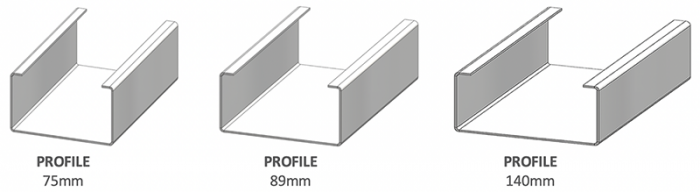
Profile Information | |||||
---|---|---|---|---|---|
Profiles | Web | Flange | Lip | Gauge | Strip Width |
C75 | 75mm | 40-50mm | 8-13mm | 0.7 - 1.6mm | 177mm |
C89 | 89mm | 40-50mm | 8-13mm | 0.7 - 1.6mm | 191mm |
C140 | 140mm | 40-50mm | 12.7mm | 0.7 - 1.6mm | 248mm |
Optional Profiles (Additional Tool Stations) or can be ordered at a later date | |||||
C100 | 100mm | 40-50mm | 12.7mm | 0.7 - 1.6mm | 258mm |
C150 | 150mm | 40-50mm | 12.7mm | 0.7 - 1.6mm | 258mm |
C200 | 200mm | 40-50mm | 12.7mm | 0.8 - 2mm | 308mm |
Technical Specification | |
---|---|
Model | SFS-International MP200 Series Framer |
Function | Framing & Truss Structures |
Typical Production Speed | 280-750 Metres/Hr Design Dependent |
Line Speed | 2,700 Metres/Hr (not production speed) |
Machine Operating System | FrameWare Software |
CADesign Software | Vertex BD Software | StrucSoft MWF Solutions |
Industrial Touch Screen | 17inch Screen PC Windows Operating System |
Data Input | USB Plug - USB Stick |
Multi-Task Operations | Add | Modify | Cancel Production |
Production Graphics | All Operations shown in real time |
Production Options | Batch or Single Profile Production |
Data Storage | System Save Off Auto Save - Zero Waste |
Ambient Air Temperature | Operating Range 0-35Deg C |
Machine Data | |
---|---|
Machine Chassis | CNC Machined Box Structure |
Power Transmission | Geared |
Roll Forming Stations | 11 Roller Profile Forming Sets |
AC Geared Motor | Drive Power Capacity 15kW |
VFD Synchronised | State of the Art Control System |
Hydraulic Pump Motor | Motor Capacity 11kW (15HP) |
Framer Power Supply | 36kW | 45A | MCCB 60A |
Mains Electrical Supply | 3phase, 415v | 50-60Hz | N+E |
Hydraulic Tank Capacity | 100 Litres |
Hydraulic Cooling System | Radiator with Auto Operation Fan |
Inkjet Profile Printer | Mathews Mperia Lite OEM |
Gauge Adjustment | Auto Adjustors on Roller Sets |
Self Lubricating | Steel Coil Lubricating System |
Physical Data | |
---|---|
Length | 7400mm |
Height | 1650mm |
Width | 1250mm |
Machine Weight | 6,100Kg (approximately) |
Production Footprint | 16.4Metre length x 1.3Metre |
SFS MP200 Multi-Profile Framer
MULTI-PROFILE SYSTEM | FRAMES, TRUSSES, BEAMS, FLOOR JOISTS (0.8 - 2mm) (Imperial 22 - 14gauge)
Profile Widths 75mm | 89mm | 140mm | 200mm
High speed manufacturing with the capability to produce three (3) profiles ranging in thickness from 0.8mm to 2mm for all your frames, trusses and floor joists enabling the LGS Manufacturer to deliver a wide range of construction projects, from bathroom pods
to multi-level buildings
The SFS MP200 Framer has all of the manufacturing operations & features of our well proven and very reliable SFS SP160 Single Profile Series Framers
SFS MP200 FRAMER | INNOVATIONS
- End Bearing Studs is a very unique and important feature that to ensure code
compliance that Engineers require, that is true load end bearing frame vertical
connections. - Well defined & precise profile shape and deep dimple design ensures that
connection screws/rivets are flush with the profile flanges, resulting in the wall
lining board sitting flush against the frames. - Rolling Bay profile width change fully automatic option by selecting the profile width
on the touch screen, the servo motor drive adjusts the rollers to the precise
width in less than 2 minutes. Or you can order the standard manual specification - The Operator in less than 20 minutes with either the Automatic or Manual operation completes the profile width changeover while the new width steel coil is loaded on the De-Coiler
- The MP200 Multi-Profile Framer is engineered with simplicity in mind to keep maintenance & servicing costs minimal and deliver the most cost effective capital investment to the LGS manufacturer.
- No specialised automation skills or qualifications are needed to operate, maintain
and service your MP200 Multi-Profile Framer

Automatic Rolling Bay Servo driven Changeover
- The Operator selects the Profile width at the Framer Touch Screen
- The Servo Motor Drive automatically changes to the new profile width
- Precise and fast changeover of the Rolling Bay in less than 8 minutes
Reliable Technology Built to Last
“Precision Accuracy with Zero Tolerance and High Volume Production ”
-
- Fast, reliable and very accurate steel frame manufacturing solution by SFS International resulting in very cost effective design & build technology
- SFS International have a reputation for manufacturing well engineered, industrial grade Framers to International standards built with ease of maintenance in mind
- SFS International Framers are designed and built with high quality International
electronic components and electrical systems
Framer Features | |
---|---|
![]() |
Thirteen (13) roller sets in the rolling bay to precisely cold roll the steel coil strip into the C Channel Profile into a shape with well defined radius's to the web, flanges and lips. |
![]() |
Rail mounted hydraulic lines made accessible for visual routine check & ease of maintenance of all tool station operations, the Operator requires no specialist skills to identify and service when required |
![]() |
Sensors regulate the Framer Performance so the operations of all Tool Stations are optimised for maximum production and the condition of working components are constantly monitored. |
![]() |
Auto Gauging of the Rollers to adapt to the steel gauge loaded into the Framer without the Framer Operator having to manually adjust all the roller settings individually after loading a different gauge steel |
![]() |
Geared Rolling Bay all profiling rollers are driven by precision machined hardened gears to ensure long life performance & accurate positioning in excess of half a million metres with minimal service & maintenance |
![]() |
Individual Hydraulic Cylinders & Tool Stations cylinder mounted actuating solenoids & valves, accessible hydraulic lines, and individual tool stations for simplified maintenance by your Framer Operator |
![]() |
Automatic Track Manufacture at high speed producing U Channel profiles for True Track & Stud production, Truss & Beam profiles, with wider flanges for ease of frame assembly |
Motorised De-Coiler | |
---|---|
Automatic Feed | Motorised Power Drive |
Pressure Arm | Pneumatically controlled to restrain the steel coil |
Maximum Width Coil | 320mm Coil Strip Width |
Coil Inner Diameter Hub | 460 - 520mm Dia |
Maximum Outer Coil | 1200mm Dia |
Maximum Loading | 3,000Kg |
Hub Arms | Manual Expansion |
Hydraulic Expansion Option Available | |
Motor Power | 2.2kW |
Power Supply | Three phase | 50-60Hz supply via the Framer |
De-Coiler Physical Data | |
---|---|
Length | 750mm De-Coiler Body 1200mm with Steel Coil |
Height | 750mm Body 1950mm inc Pressure Arm |
Width | 1000mm |
De-Coiler Weight | 700Kg (approximately) |
Positioning the De-Coiler | |
---|---|
Between Framer & De-Coiler | Allow a minimum spacing of 4Metres |
De-Coiler Key Features
“Steel Coil up to 3 Ton Capacity with Auto-Feed Operation”
-
-
- A Optional Hydraulically operated Hub is available for expanding and contracting the Hub to clamp the Steel Coil when loading and removing a Steel Coil instead of this being a manual operation
- Automatic Variable Speed Control of the steel coil feed into the Framer
- Pneumatic pressure arm to restrain the steel coil end from un-raveling to prevent potential injury when loading/un-loading
- Mains supply & control cable to the De-Coiler via a plug/socket at the Framer, a separate electrical supply is not required
- When positioning the De-Coiler the hub can be either left or right sided (shown with the hub on the right side) for loading of the coil
“Pressure arm for Health & Safety of the Operator ”
-
Standard Operations for all (3) Profiles | ||
---|---|---|
Tool Station | Automated Hydraulics | |
Operations (9) | Description of Profile Operations | |
1 | Track & Stud | Automated Track Width change for effortless Stud Insert |
2 | 13mm Dia Bolt Hole | For Bottom Plate Anchor Bolts or bolting Frames together |
3 | 3.5mm Dia Web Holes (2) | Index Holes for locating Frame to Frame Fixing Screws |
4 | 33mm Dia Service Hole | Hole through Frame Profile Web for Services |
5 | End Chamfer | 45Deg Chamfer at the end of Truss or Beam Web Members |
6 | Dimple Connection Holes | Dimpled 3.5mm Dia connection holes for flush Fixings |
7 | Web Notch | For Single & Continuous Nogs |
8 | Lip Notch | Lip cut to permit inserting a Profile into another Profile |
9 | Shear | Part Cut or Full Cut Guillotine Shear |
Automated Tool Operations
- CADesigner selects the position of the service holes for MEP Services in any profile
- The Engineer can instruct where the position of Frame to Frame perimeter stud connections holes should be placed to meet code compliance
Profile Connections | |
---|---|
Dimpled Flange Connection | 3.5mm Punched Hole |
Bolt & Anchor Bolt Hole | 13mm Dia (can be customised) |
End Truss Notch | 45Deg Chamfer Truss Cut |
Web Index Holes (2) | Frame to Frame Screw Connections |





